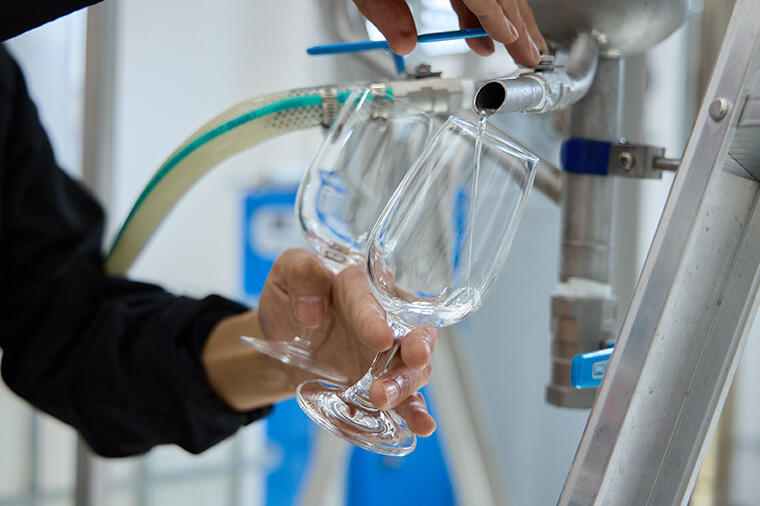
ウイスキー蒸留所のシンボルともいえるポットスチルの完成形が、ついに白日の下に!現地への搬入に先立って、文字通り南国福岡の陽光が照り付ける中、オープンエアで行われた装置組み立てと試運転の模様を実況する。
「ポットスチル完成!蒸留装置がすべて揃いました!!」
北軽井沢蒸留所計画の新たな進捗を知らせるメールが、オーナーの坂本龍彦さんから届いたのは2022年秋口の頃。夏に“へら絞り”のスチルヘッド完成を見届けてから、さらに2ヶ月が経っていた。
北軽井沢では既に建屋の大部分が完成し、プラント工事の準備を進めようという段階に。現場での据付と配管を行う前に、蒸留釜、冷却器、両方を連結するパイプがワンセットになった状態で正常に作動することを確認する必要がある。ついては、仮組み立てとボイラーの試運転を福岡で行うことになったという。
図面ではない実物の蒸留装置の全容を目にするのは、坂本さん、設計の川波宇澄さんの両者にとっても初めてのこと。お披露目にも等しい機会とあって、わくわくと弾む気持ちが、メールの文面からも伝わってきた。
組み立てが行われたのは、福岡市街から20kmほど北上した古賀市にある「安谷製作所」。配電盤や店舗看板、ステンレス家具など、幅広い産業用設備の製造実績をもつ創業65年の金属加工メーカーだ。
坂本さんの現場到着と同時に、まずは工場内で銅のスチルヘッドとステンレスタンクを連結する作業からスタート。見覚えのある流線型の銅製ヘッドには、ビスの付いたステンレスのフランジが装着されている。この部分をボイルタンクと完全に繋ぐことで、初めてポットスチルが蒸留釜としての機能を持ちうるのだ。
「銅とステンレスの溶接は難しいんです」と打ち明けるのは、製作を統率した取締役営業部長の安谷啓二さん。
「融点や硬度が違ううえに、ステンレス表面の酸化防止用の被膜が接合の邪魔になることもある。もともと相性がよくないので、独自の溶接方法を工夫する必要があるのです」
接合が完了したポットスチルは、クレーンを使ってフォークリフトに載せ、戸外に。ここからは川波さん、安谷さんにCAD設計を担当した今石毅さんが加わり、足場をひらりひらりと身軽に移動しながらネック、ラインアーム、コンデンサーの順に繋いでいく。
一方、下から作業を見上げる坂本さんは、指示を出しながらネックの角度チェックに集中。
「アームの向きがスピリッツの特徴に影響を与えるので、ネックの角度はけっこう大事なポイントで。ウォッシュの量や加熱温度など、バッチごとの条件に合わせてアームの向きを調節しやすい構造に仕上げてもらっているんです」
こうしたクライアントのリクエストにも、チーム福岡の3人は持ち前の好奇心と熱量とスキルを総動員して応えてきた。川波さんを中心にいくつものプロジェクトでチームを組んできたパートナー同士。私生活でも交流の多い盟友であり、ハーブ用蒸留装置でも多くの“共作”を創出してきた3名の息はぴったり。
「ウイスキーの(蒸留器)はつくったことも見たこともなかったけれど、みんなお酒が好きだから。まあ、楽しい仕事だったよね」と言い合う様子も微笑ましい。
早朝から始まった組み立てが終わり、水を通しながらのボイラーチェックを含むすべてのテストが終了したのは正午過ぎ。雲ひとつない青空を背景に、すっくりと誇らしげにそそり立つポットスチルを、揃って安堵の表情を浮かべた4人が見上げている。それは、未知の空に向かうロケットの旅立ちを見守り、送り出す祈りの姿にも見えた。
文:堀越典子 撮影:石井小太郎